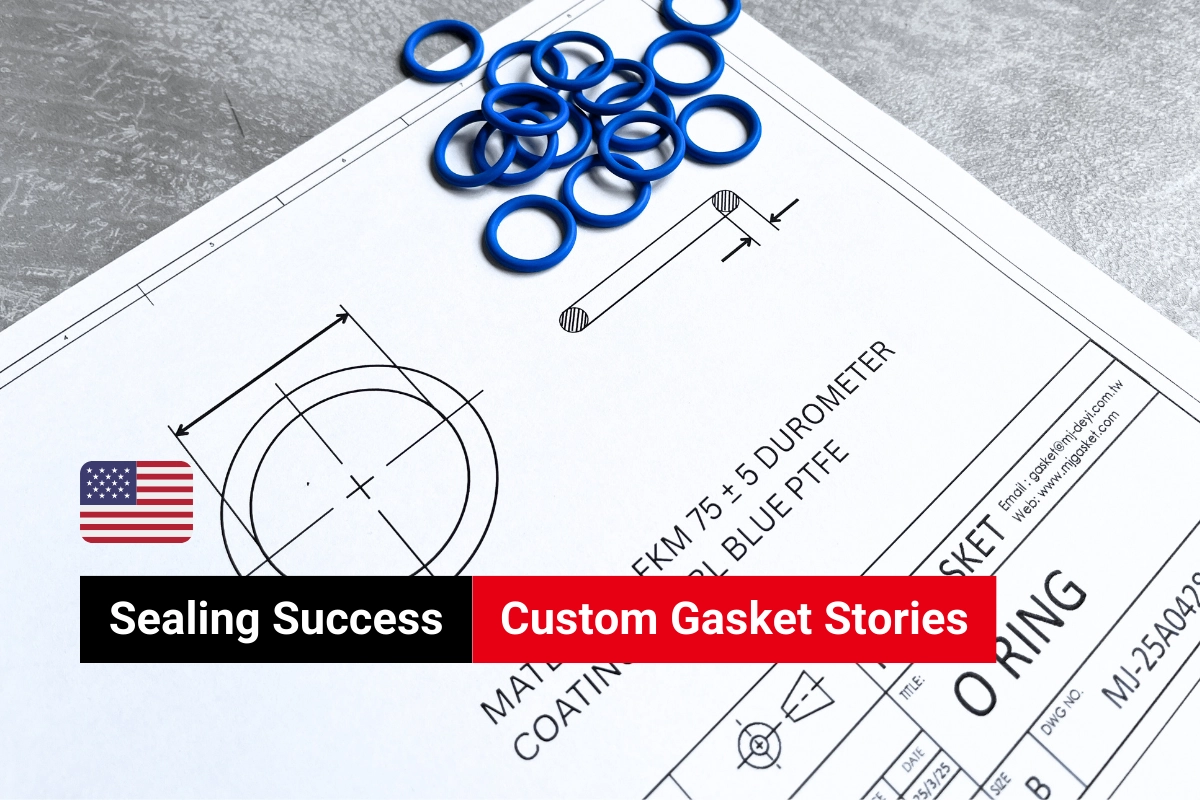
Case ID: MJ-CS-16-004
MJ Gasket provided a custom solution for a US-based client in need of a specialized O ring with Teflon coating. The O ring was tailored to meet specific functional requirements, with an emphasis on improving surface characteristics and ensuring long-term sealing performance. With our experience in material selection and precision manufacturing, we delivered a dependable and durable O ring solution suited to the client’s application.
In this case study, we are going to share more information about O rings and Teflon coating, and how they work together to enhance sealing performance.
What is an O Ring?
An O ring is a mechanical gasket in the shape of a torus, typically made from elastomer materials such as NBR, FKM, EPDM or Silicone. It is designed to be seated in a groove and compressed between two or more parts to create a tight seal. O rings are widely used due to their simple structure, low cost, and effective sealing capabilities. Their versatility allows them to be customized in terms of size, material, and coating—like the Teflon-coated version featured in this case.
What is an O ring used for?
O rings are commonly used in engines to prevent leaks of oil, fuel, coolant, and air between metal components. Within an engine system, O rings can be found in fuel injectors, oil filter housings, turbochargers, and more. They play a critical role in maintaining pressure and keeping fluids contained, even under high temperature and pressure. A properly selected and manufactured O ring—like the one in this case study—helps ensure engine efficiency, prevent fluid mixing, and reduce maintenance needs.
What is the purpose of o ring and valve seals in a cylinder head?
In the cylinder head, O rings create a tight seal between components, preventing the leakage of fluids and maintaining proper pressure within the combustion chamber. Valve seals, which also play a crucial role in the cylinder head, ensure that oil does not leak into the combustion chamber, preventing burning oil and maintaining combustion efficiency. O rings and valve seals work together to keep fluids contained and ensure optimal engine performance, even under high temperature and pressure.
O Ring Material
Selecting the right O ring material is essential for ensuring effective sealing and durability in various applications. O rings are widely used in industries like automotive, aerospace, and manufacturing, thanks to their simple design and reliable performance. FKM (Viton®) is a popular choice for O rings due to its resistance to a broad range of chemicals, oils, and high temperatures. Nitrile Rubber (NBR) is another common material, favored for its excellent resistance to petroleum-based fluids such as oils and fuels. EPDM is well-suited for applications that involve water, steam, and certain chemicals, offering excellent resistance to weathering and ozone. Silicone O rings are ideal for high-temperature applications and offer good flexibility at low temperatures.
What O Ring Material is Best for Different Applications?
The best O ring material depends on the specific needs of the application. FKM (Viton®) is highly versatile and works well in environments with exposure to oils, fuels, and high temperatures, making it ideal for automotive and industrial applications. Nitrile Rubber (NBR) is a great option for sealing oils, fuels, and hydraulic fluids, while EPDM is often used in systems with water, steam, or low-pressure chemicals. For applications that require flexibility at low temperatures or high-performance, Silicone O rings are an excellent choice. Additionally, for applications that require high chemical resistance, PTFE (Teflon®) coated O rings offer enhanced durability and sealing performance. The material selection depends on factors like fluid type, temperature range, and exposure to various environmental conditions.
Teflon O Ring
What is Teflon® (PTFE)?
Teflon®, also known by its chemical name Polytetrafluoroethylene (PTFE), is a high-performance plastic known for its exceptional resistance to chemicals, high temperatures, and friction. Originally developed for industrial applications, Teflon has become widely used in sealing components like O rings due to its unique non-stick properties and ability to perform under harsh conditions.
Why Use Teflon for O Ring?
Teflon O ring—or PTFE-coated O ring—is especially valuable in demanding applications that involve aggressive chemicals, extreme temperatures, or high-speed movements. While Teflon itself isn’t as elastic as rubber, it can be used as a coating over elastomer cores (such as FKM or NBR), combining the flexibility of rubber with the protective benefits of Teflon.
This combination enhances the O ring’s ability to resist wear, reduce friction, and extend sealing performance. Teflon-coated O ring is commonly found in fuel systems, chemical processing, food and pharmaceutical equipment, and hydraulic systems where both chemical resistance and long-lasting durability are required.
How to Work with MJ Gasket for a Custom Teflon-Coated O Ring?
Getting started is easy. You can provide us with a technical drawing that includes the inner diameter (ID), cross-section dimensions, rubber type, hardness, and your preferred Teflon (PTFE) coating color. If a drawing isn’t available, simply let us know the AS568 standard size, the rubber material (such as FKM or NBR), and the coating color you need. Our team will review the details and assist you with material selection, coating options, and production feasibility to ensure a durable and high-performing O ring tailored to your application.