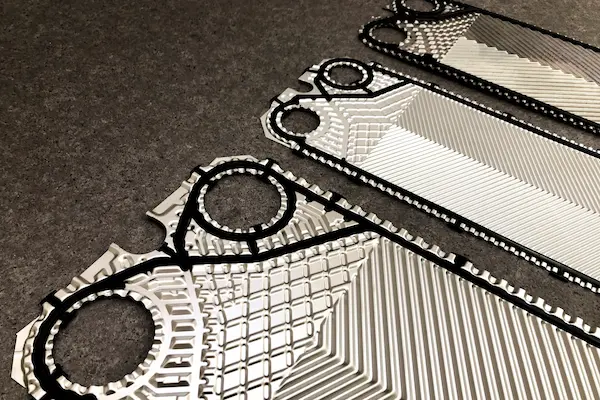
Dive into the world of Plate Heat Exchanger (PHE) gaskets with our comprehensive introduction. Uncover their crucial function, explore various materials, and learn about MJ Gasket solutions in this informative piece. Trust MJ Gasket for high-quality gaskets backed by over 40 years of expertise.
Table of Contents
Brief introduction of Plate Heat Exchanger
Plate heat exchangers (PHE) are widely used for various fields. It’s an equipment that transfers heat between two fluids by using metal plates to spread out the fluids over a large surface area. PHEs are made up of several plates that are held together by a fixed plate and a loose pressure plate. Each plate has a gasket arrangement that creates two separate channel systems.
For more detailed information, please check here for clear and complete understanding the information.
Understanding the Role and Functionality of PHE Gaskets
Gaskets in PHE come in different types, such as diagonal flow gaskets, parallel flow gaskets for channel plates, and end plate gaskets. Each type is designed to suit specific plate configurations and fluid flow patterns within the heat exchanger.
The selection of the appropriate gasket material depends on factors like operating temperature, fluid compatibility, and environmental conditions. Manufacturers carefully choose materials that can withstand the conditions encountered in various applications while maintaining a reliable seal.
Proper installation and maintenance of PHE gaskets are essential to ensure their longevity and effectiveness. Regular inspection, replacement as needed, and adherence to manufacturer guidelines for installation are crucial steps in maximizing the performance of PHE gaskets.
In summary, understanding PHE gaskets is paramount for optimizing the efficiency and reliability of plate heat exchangers across different industries. By selecting the right gasket material and ensuring proper installation and maintenance, users can enhance the performance and longevity of their PHE systems.
You can see how easy to install the PHE gaskets with this video, to demostrate the gasket maring surface for PHE.
Exploring Various Materials for PHE Gaskets
The main materials used in PHE (Plate Heat Exchanger) gaskets are typically elastomers or synthetic rubbers. These materials are chosen for their flexibility, resilience, and ability to maintain a tight seal under varying temperatures and pressures. Some common elastomers used in PHE gaskets include:
- Nitrile rubber (NBR): Known for its excellent resistance to oils, fuels, and chemicals, making it suitable for a wide range of industrial applications.
- EPDM (Ethylene Propylene Diene Monomer): Offers good resistance to heat, weathering, and ozone exposure, making it ideal for outdoor and marine applications.
- FKM: Provides high temperature resistance and chemical compatibility, making it suitable for demanding environments where aggressive fluids are presents.
- Rubber: Known for its excellent temperature resistance and flexibility, making it suitable for high-temperature applications.
The specific material chosen for a PHE gasket depends on factors such as the operating temperature, type of fluids being processed, and environmental conditions. MJ Gasket select materials that offer the best combination of properties to ensure optimal performance and longevity of the gasket in the given application.
What type of PHE gaskets does MJ Gasket offer?
At MJ Gasket, with over 40 years of expertise in heavy-duty engine gaskets, we also specialize in high-quality PHE gaskets. Our commitment to the perfect fit is exemplified in our mission. Guided by the vision ‘Develop Nonstop,’ we stay curious, embracing new products and knowledge. Explore our best-selling PHE Gaskets with below famous brands such as MTU, Cummins, Caterpillar, Alfa Laval, Detroit Diesel..etc.
MTU Marine Engines
Cummins Marine Engines
Caterpillar Marine Engines
For comprehensive Plate Heat Exchanger Gaskets, trust MJ Gasket’s and commitment to quality.
MJ Gasket’s dedication to excellence, backed by over four decades of experience, has resulted in high-quality gaskets that are now a promising product in the market. We’ve assisted numerous customers in expanding their businesses by providing top-notch gaskets. Our commitment to quality is underscored by the prestigious ISO 9001:2015 certification held for seven consecutive years, making us a certified gasket manufacturer recognized by GFA. Contact us for details.